Chemical Toughening
We always strive for the highest quality of our products to match the high expectations and requirements of our various customers. TILSE® GLASS is therefore chemically toughened to guarantee the best optical quality without any distortion such as local shading or changes in colour known from thermally toughened glass.
As the process step of chemical toughening plays a key role for the quality of TILSE® GLASS, we operate this process step in-house in our own chemical bath.
Learn more about the process of chemical toughening, the benefits compared to thermal toughening and our chemical toughening service for customer owned glass (COG).
Chemical Toughening of customer owned glass (COG)
We offer chemical toughening as a personalized service for customer-owned glass (COG). Our state-of-the-art chemical bath can accommodate glass panes up to a maximum size of 6 x 2.70 meters. Choose TILSE for your glass toughening needs. With our cutting-edge technology and expert team, we ensure that your glass is not only aesthetically pleasing but also meets the highest standards of strength and safety.
Contact us to learn more about our chemical toughening services and how we can assist in bringing your visionary projects to life.
TILSE® GLASS is always chemically toughened to guarantee the highest quality of glass in the market.
The Chemical Toughening Process of Glass
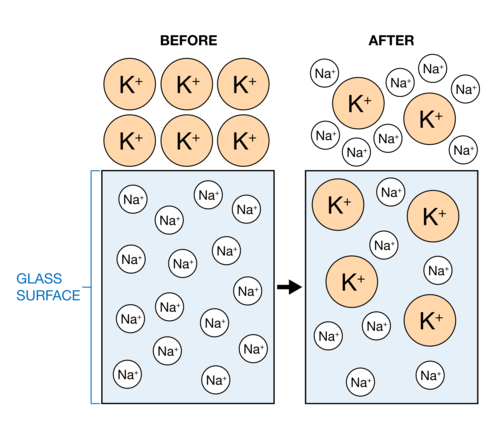
Chemical toughening of glass is an advanced process that significantly enhances the strength and durability of glass products. Unlike traditional methods such as thermal toughening, chemical toughening involves a unique ion exchange process that alters the physical properties of the glass at a molecular level. Here's how it works:
Preparation of the Glass: The process begins with the preparation of the glass, which is cleaned thoroughly to remove any contaminants that might affect the treatment.
Ion Exchange Process: The core of chemical toughening is the ion exchange process. The glass is submerged in a bath of chemically pure and highly selected molten potassium nitrate (KNO3) at temperatures ranging from 380°C to 450°C. During this stage, smaller sodium ions (Na+) in the glass surface are replaced by larger potassium ions (K+) from the salt bath. This exchange occurs because the potassium ions have a larger ionic radius compared to the sodium ions.
Creation of Compressive Stress: As the larger potassium ions replace the smaller sodium ions, they occupy more space, which generates a layer of compressive stress on the surface of the glass. This layer can extend up to a depth of about 100 micrometers.
Cooling and Finishing: After the ion exchange, the glass is slowly cooled to room temperature. This controlled cooling process is crucial to maintain the integrity of the newly toughened surface.
Quality Inspection: The final step involves a thorough inspection of the glass to ensure that it meets the required strength and quality standards.
The result of this process is a glass that is significantly tougher and more resistant to thermal and mechanical stress than standard glass. It becomes less prone to cracking and breaking, and even in the rare cases of breakage, it tends to crumble into small, granular chunks rather than sharp shards, offering a safety advantage over traditional glass.
Advantages of chemical toughening
Chemically toughened glass has a lot of advantages compared to thermally toughened glass
Increased Strength
- Chemical toughening results in a stronger glass as the ion exchange process creates a deeper layer of compressive stress on the glass surface.
- This makes the glass more resistant to physical impacts and pressure.
Improved Thermal Stability
- Chemically toughened glass has a higher resistance to thermal stress and temperature fluctuations.
- It is less likely to crack under extreme temperature changes, making it suitable for environments with varying temperatures.
Better Optical Clarity
- The chemical toughening process guarantees the best quality without any optical distortions whereas the thermally toughening process leads to optical distortions such as waviness, cloudiness or changes in colour that are visible at an acute angle or through sunglasses with polarizing lenses.
- Chemical Toughening results in clearer, distortion-free glass, ideal for applications where visual clarity is crucial.
Customization and Precision
- Chemical toughening allows for more precise control over the toughening process, offering a higher level of customization in terms of glass strength and performance.
- This precision is particularly beneficial for specialized applications requiring specific glass properties.
Reduced Weight
- Chemically toughened glass can be made thinner than thermally toughened glass while retaining similar strength characteristics, leading to lighter overall weight.
- This aspect is advantageous for applications where weight is a critical factor.
Environmental Impact
- The chemical toughening process often has a lower environmental impact compared to thermal toughening, which requires high energy consumption due to the intense heat needed.